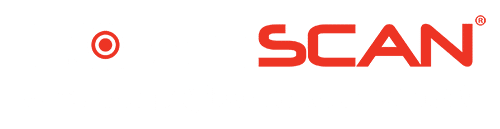
Maximisez les facteurs de camionnage sur votre mine. Améliorez vos bénéfices nets.
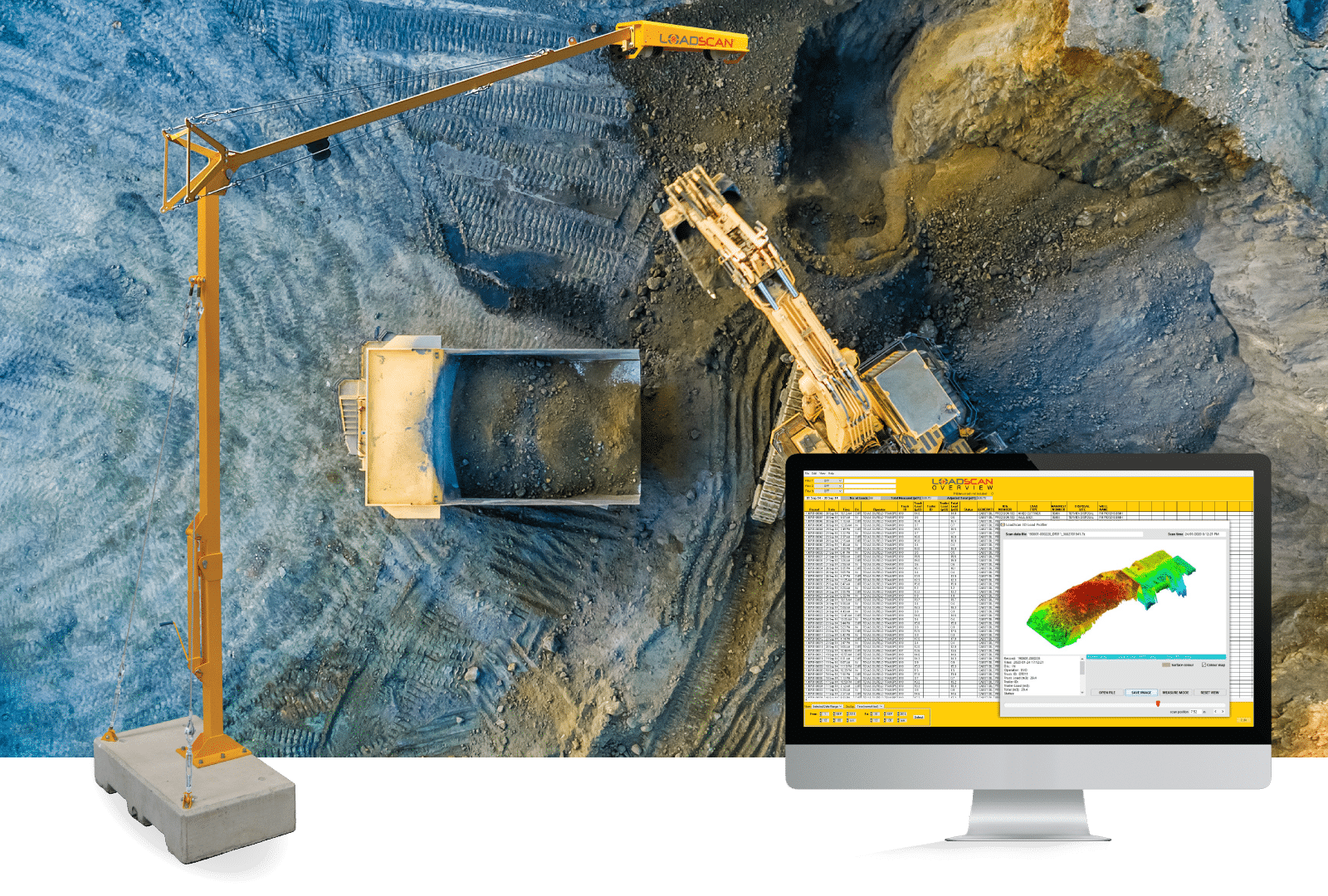
Les "facteurs de camionnage" sont un terme collectif utilisé dans l'industrie minière pour décrire les différents éléments liés à l'utilisation et au déploiement des camions. En fin de compte, le coût par tonne transportée est le facteur clé qui affecte la rentabilité. Il est influencé par de nombreux sous-facteurs qui peuvent être suivis indépendamment.
Le principal facteur qui influence et détermine le coût par tonne transportée est le volume réel mesuré de matériaux chargés dans la benne d'un camion par rapport à la capacité nominale de charge utile du camion, telle qu'elle est spécifiée par le fabricant. L'utilisation de la capacité a une relation directe avec les coûts d'exploitation, les camions sous-utilisés augmentant les coûts d'exploitation et le coût par tonne transportée.
D'après notre expérience, certaines mines utilisent la capacité de charge nominale comme mesure de toutes les charges, tandis que d'autres peuvent utiliser un facteur de sous-charge moyen estimé (par exemple 5 %) pour mesurer et prendre en compte les matériaux déplacés par leurs camions. Bien que ces deux systèmes soient simples à appliquer, ils ne fournissent pas une mesure précise des matériaux réellement déplacés, livrés à l'usine ou stockés. Dans les deux cas, la précision peut être considérablement compromise, ce qui complique l'établissement des rapports et la planification.
Prenons l'exemple d'une mine équipée de cinq camions de 60T, chacun effectuant 10 chargements par équipe, 3 équipes par jour. Le total des matériaux déplacés à capacité nominale est de 9 000 tonnes par jour (3,285 millions de tonnes par an). Si vous appliquez un facteur de sous-charge moyen prudent de 5% à la capacité de 60T, vous obtenez une charge utile moyenne de 57T par camion. Il en résulterait que 3,121 millions de tonnes seraient effectivement transférées chaque année, soit une réduction significative par rapport à la capacité nominale (-164 000 tonnes), ce qui représente près de 2 900 voyages supplémentaires par an.
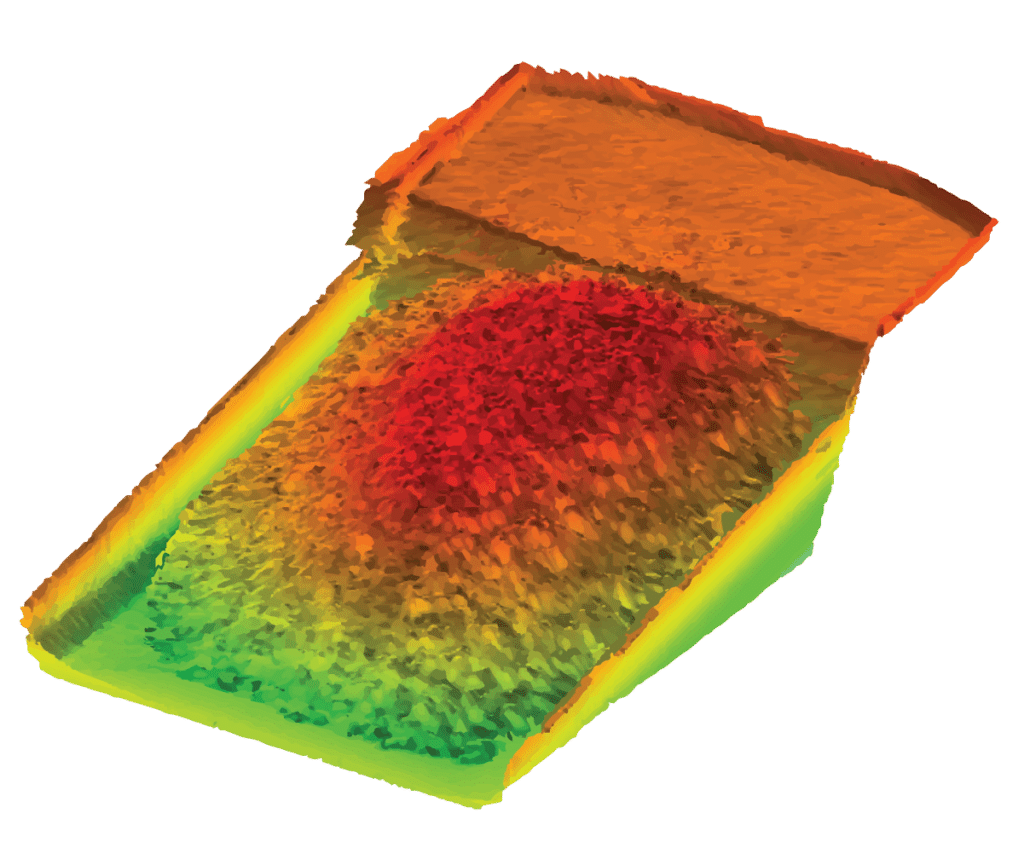
Sous-chargé
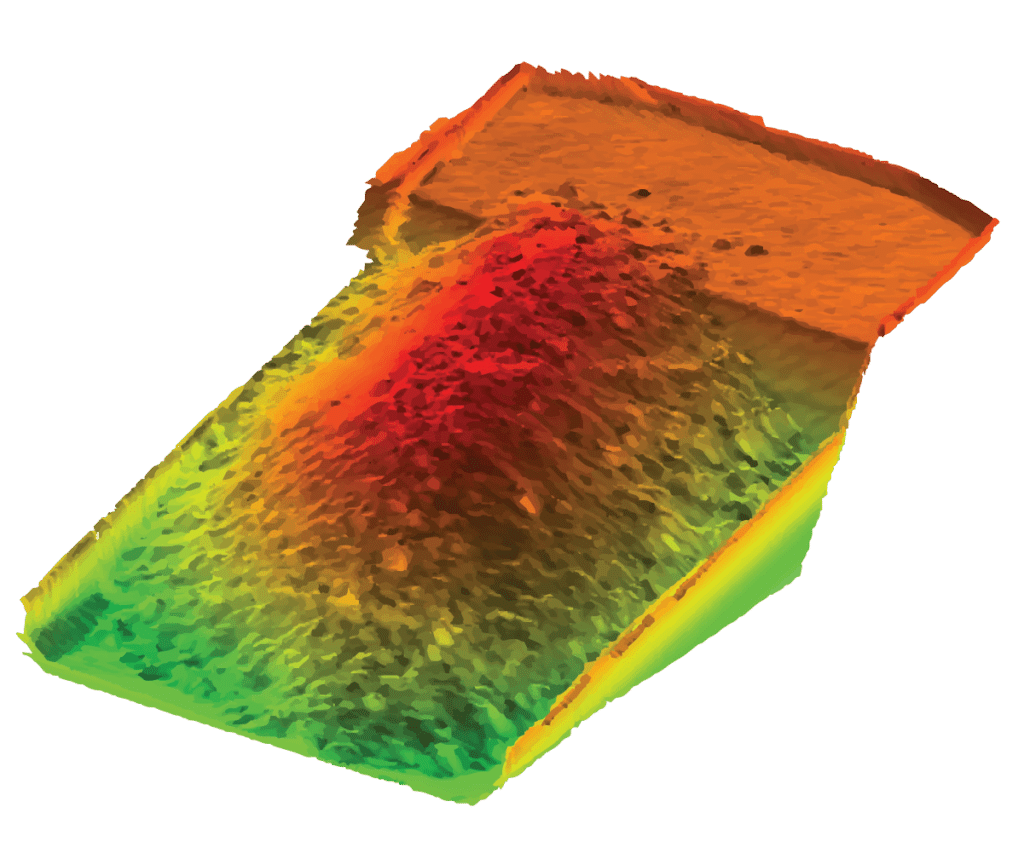
Chargement optimal
D'après les études d'audit de charge sur site que nous avons menées et les résultats de mesure des scanners LVS installés, nous constatons généralement que les camions des mines sont en moyenne sous-chargés de 5 à 15 %, voire de 20 à 25 % dans les cas les plus graves. Cela peut avoir d'énormes répercussions sur la production et les finances d'une entreprise qui exploite des matériaux de toute valeur, même des morts-terrains de faible qualité.
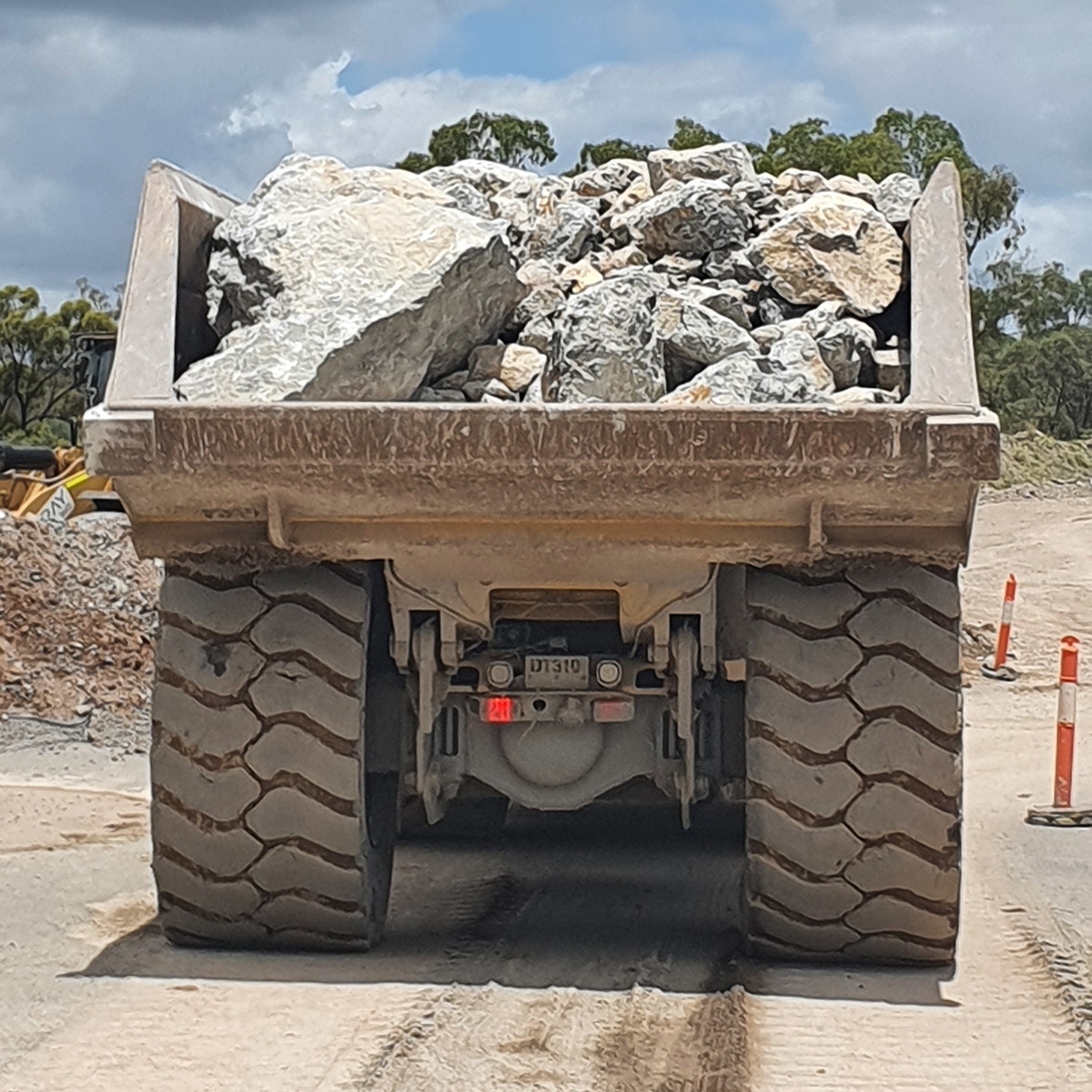
L'exemple précédent est basé sur le poids en tonnes des matériaux déplacés (les mines traitent généralement en poids et non en volume). Vous vous demandez peut-être pourquoi vous utiliseriez un scanner mesurant le volume cubique et non un pont-bascule pour mesurer les charges de camion, et comment un scanner volumétrique peut améliorer les facteurs de camionnage.
Dans certaines mines, un seul camion est équipé d'une balance embarquée, qui est étalonnée en permanence. D'autres mines disposent d'un ensemble de balances placées sur le côté de la route, qui pèsent les camions par intermittence pour vérifier leur chargement. En général, elles n'arrêtent pas tous les camions sur le pont-bascule, car c'est trop lent et cela peut réduire la productivité d'un ou deux chargements par équipe. L'autre problème lié à l'utilisation de ponts-bascules est que les ponts-bascules enterrés nécessitent beaucoup d'entretien de routine (c'est-à-dire des temps d'arrêt). Les systèmes de pesage dynamique peuvent également être imprécis.
Dans ce cas, comme ils n'utilisent pas de système de pesage pour chaque chargement, ils appliqueront un facteur de camionnage standard à chaque chargement terminé, ce qui est inexact et entraîne des divergences importantes entre le service de transport (ou l'entrepreneur) et l'usine (ou l'usine de traitement). Par exemple, le service de transport peut déclarer avoir livré 400 tonnes à la plate-forme ROM (Run Of Mine). Lorsque l'usine de traitement traite le matériau, elle peut le peser à 360 tonnes, soit 10 % de moins que ce qu'elle aurait payé au service de transport ou à l'entrepreneur.
L'utilisation du Loadscan LVS présente des avantages et des gains significatifs qui peuvent augmenter les facteurs de transport, la productivité et les résultats nets.
Le LVS mesure le volume, mais il peut le convertir en poids de tonne sur la base d'un facteur de densité en vrac connu. Des facteurs de densité en vrac précis pour chaque qualité de matériau peuvent être établis et vérifiés en faisant passer un camion sur la bascule ou en utilisant la bascule embarquée pour obtenir le poids du matériau, puis en effectuant un calcul de facteur par rapport à la mesure de volume générée par le LVS, c'est-à-dire Tonne/Volume = densité en vrac (60T/32m3 = 1,875 facteur de densité en vrac). En d'autres termes, 1m3 pèse 1,875T. Ainsi, si le matériau transporté a un facteur de densité en vrac de 1,875, le camion de 60 tonnes devrait transporter 32 m3 de matériau.
La mesure du volume est complémentaire à la mesure du poids avec des balances. En combinant le poids et le volume, la mesure des densités en vrac et des charges utiles des matériaux est plus précise.
Lors d'une récente installation minière, nous avons mesuré trois camions (60T/32m3 de capacité de trémie) après avoir mis en place le système LVS. Les charges mesurées étaient respectivement de 28,5 m3, 29,8 m3 et 24,3 m3, soit une moyenne de 27,5 m3. Sur la base de ces mesures, nous avons conclu que les camions étaient sous-chargés de 14 % en moyenne.
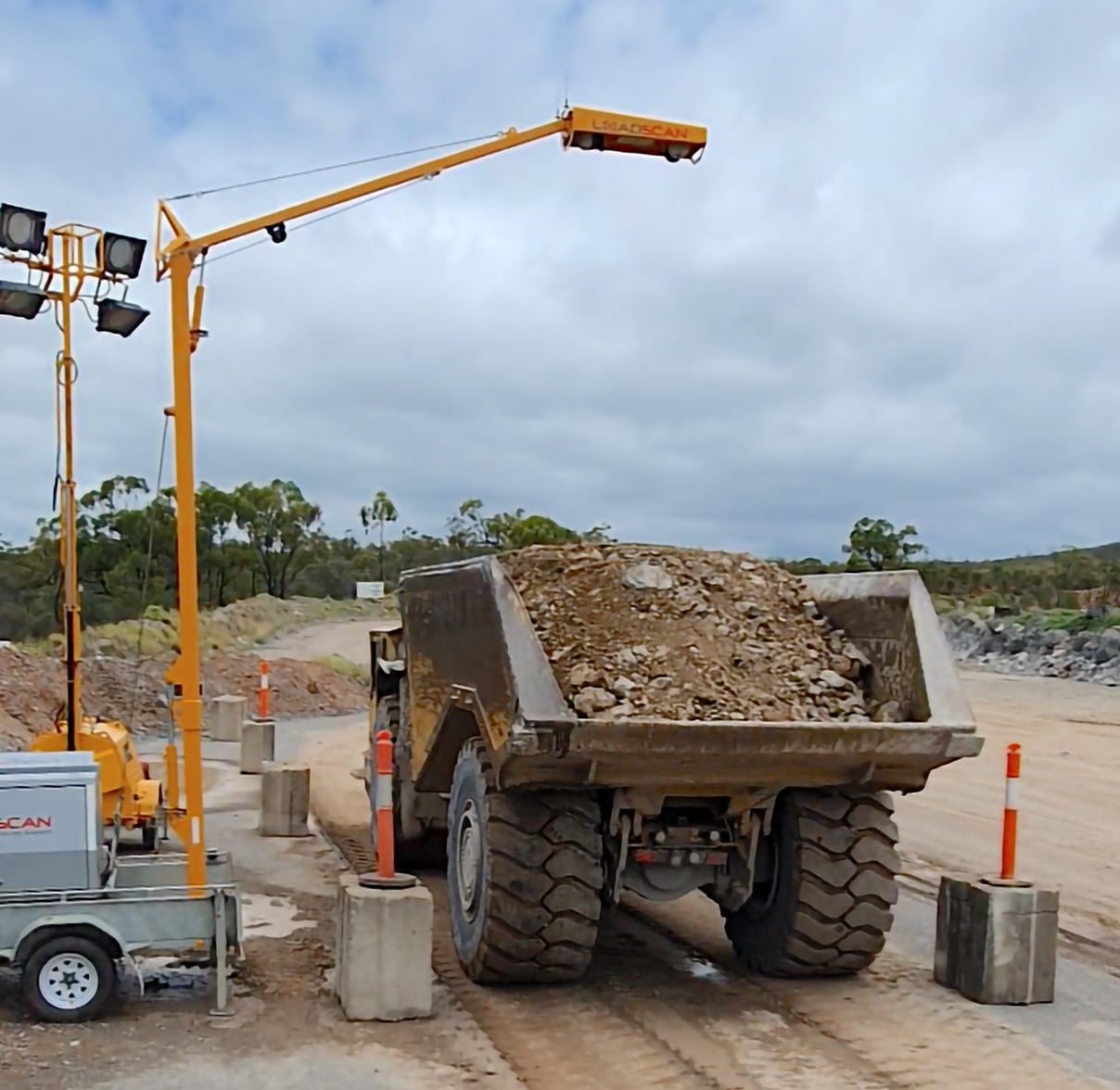
Le Loadscan LVS est un système de passage automatisé dont le résultat des mesures s'affiche en temps réel sur un tableau d'affichage à DEL. Les conducteurs voient immédiatement l'état de leur chargement et peuvent indiquer à l'opérateur du chargeur si le chargement était sous ou surchargé, ce qui permet d'éviter d'autres chargements sous-optimaux (la surcharge peut être dangereuse et augmenter l'usure du véhicule).
L'un des principaux avantages du système LVS est que les responsables des transports peuvent voir les résultats en temps réel. Dans les mines, le système LVS est généralement connecté au réseau de l'entreprise et les résultats peuvent être visualisés dans leur logiciel de gestion de la mine, ou ils peuvent utiliser notre logiciel propriétaire de rapport Overview ou le service en nuage MyScanner. Si les responsables des transports identifient des anomalies de chargement, ils peuvent prendre des mesures correctives immédiates.
Les responsables peuvent également visualiser des images 3D de chaque chargement et sauvegarder un fichier image afin de le partager avec les opérateurs de chargeurs lors des réunions de début d'équipe, ce qui permet une amélioration continue du chargement des camions. Les opérateurs de chargeurs deviennent plus conscients de leurs pratiques de chargement, sachant qu'ils sont surveillés et contrôlés par un système indépendant et irréfutable qui ne peut pas être manipulé pour donner des mesures gonflées, comme cela peut être le cas avec les balances pour chargeurs et excavateurs.
Le résultat direct de la mise en œuvre d'un scanner de volume LVS est une amélioration mesurable des facteurs de camionnage (et en fin de compte de la rentabilité).
Si vous souhaitez bénéficier de l'amélioration des facteurs de camionnage, veuillez nous contacter via notre formulaire de demande de renseignements.