Optimizing Mining Operations with Pitram and Loadscan Integration at CSA Cobar The MAC [...]
Underloading
Underloading could be costing you a fortune! We help mines optimize loading and increase trucking factors to improve profits. Read more…
Overloading
Overloading large mining trucks by as little as a 10% could substantially increase fuel consumption and CO2 emissions. Read more…
Carryback
Managing carryback to improve operations — with the Loadscan MPS. Carryback is accounted for improving accuracy of actual loads shifted. Read more…
Off-Center Loading
The hidden costs of off-centre loading — Uneven load distribution adds stress to truck components. Read more…
Inaccurate Bulk Densities
Measuring truck payloads by weight or volume — Common weighing systems are not the complete measurement solution. Read more…
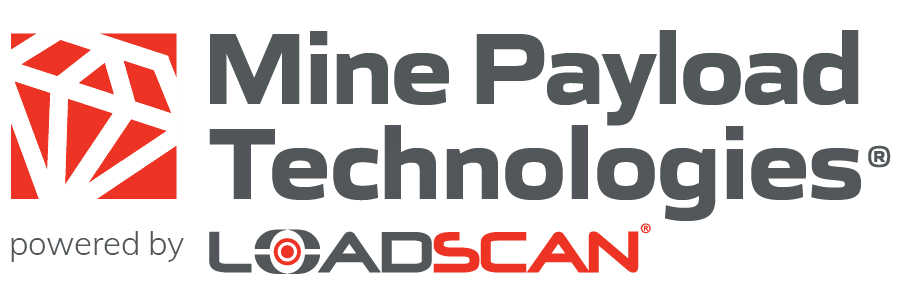
Loadscan created Mine Payload Technologies, a specialist mining division within the company, to deliver deeper insights and added-value to the sector.
Through this focused business unit, Loadscan supports the global mining sector by delivering innovative and unique mining features and enhanced capabilities that deliver measurable ROI.
Loadscan’s innovations in mining are satisfying growing global demand for reliable and accurate load measurement across a range of increasingly challenging surface and underground mining operations.
The new Mine Payload Scanner (MPS) sets a new standard for volume measurement in the industry.
Loadscan’s innovations in mining are satisfying growing global demand for reliable and accurate load measurement across a range of increasingly challenging surface and underground mining operations.
The new Mine Payload Scanner (MPS) sets a new standard for volume measurement in the industry.
A powerful non-contact and environmentally-friendly measurement system
Loadscan technology is helping our customers to reduce their carbon footprint and lessen the impact on the environment.
Fast return on investment
Mines across the globe are leveraging load volume scanning technology to maximize payloads, with most mines reporting increases in trucking factors between 5% and 25%.
A powerful non-contact and environmentally-friendly measurement system
Loadscan technology is helping our customers to reduce their carbon footprint and lessen the impact on the environment.
Fast return on investment
Mines across the globe are leveraging load volume scanning technology to maximize payloads, with most mines reporting increases in trucking factors between 5% and 25%.
Key Features
Combining eye-safe laser scanning technology with proprietary software to give seamless data integration with your systems.
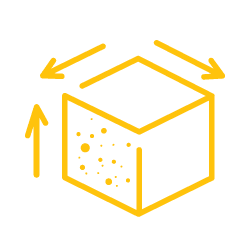
VOLUME
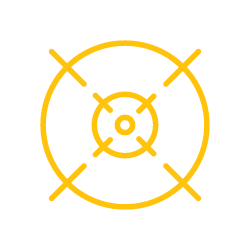
+/-1% ACCURACY
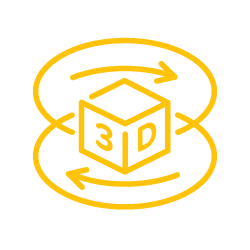
SCAN IMAGES
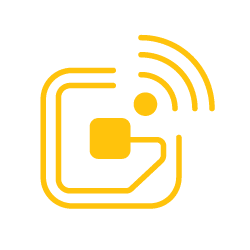
RFID TRACKING
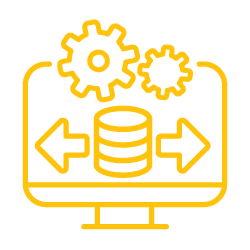
SQL / API DATA SYNC
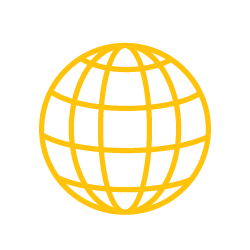
GLOBAL SUPPORT
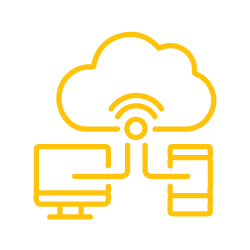
REMOTE ONLINE ACCESS