Optimizing Mining Operations with Pitram and Loadscan Integration at CSA Cobar The MAC [...]
Loadscan scales up to measure large rigid dumpers.
A common misconception about load volume scanning (LVS) systems is that they are only effective on road trucks and lighter articulated haulers.
While this may have been true in the past Loadscan is proud offer accurate load management solutions across all dump truck varieties – including the largest rigid dumpers.
This is exciting news for those operating open cut mines as it provides a data-rich, low maintenance alternative (or addition) to the on-board weighing systems currently being used.
Unlike on-board weighing systems, which require ongoing servicing and calibration, Loadscan only requires a single installation with no major earthworks or fiddly calibration. There’s no need to fit out an entire fleet (or install an expensive fixed truck scale) as a single Loadscan unit provides traceable drive-through payload measurement for all trucks that pass beneath it.
What’s more, this method of payload monitoring provides a more detailed picture of how much material is being shifted. Loadscan’s mining specific software interfaces with more office management systems than any other LVS system, accounts for haul back, , and supplies 3D profiles of every load to ensure you’re hauling optimum volumes. All from a single in-motion scan.
Case study: Checking CAT 775 payload stats in the Californian outback
Loadscan recently undertook a trial in which a scanner was deployed at a mine site whose operators wanted to check their payload capacities and optimize what they’re hauling.
At this mine, the CAT 775 trucks travel seven miles downhill from the quarry and maximum loading would result in material being dropped in transit. On paper these trucks have a maximum working payload (110%) of 77.5 tonnes. But the mine operators wanted to know the reality of their optimum payload – a measurement relevant to any mine given their individual environments.
To begin with the trucks were scanned empty to provide baseline stats in the LVS system. They were each assigned an RFID tag for automatic identification and then the trucks were driven under the scan head, on their normal downhill route, where they were automatically scanned and volume measurements recorded. The CAT 775’s loads were measured in cubic meters and converted to metric tonnes automatically using density factor supplied by the mine geologist.
From the 34 loads measured, mine management were able to see that loads from reclaim site near the crusher were significantly bigger than loads that came direct from the quarry. Loads from the quarry were smaller so that rocks did not fall onto the haul road which had the potential to cause damage to the truck tires and downtime while rocks were removed from the haul road.
They were also able to see, in real-time, that their average payload was 70.3 metric tonnes – a 10% difference from the manufacturer’s 77.5 max payload figure – which will allow them to much more accurately project mining productivity going forward and calculate the actual cost per tonne of ore shifted. The LVS also gave them the 3D visual tools to educate loader operators on effective loading of the haul trucks.
The mine’s management team were highly impressed with the Loadscan system, praising its ability to provide insightful data from a single drive through scan. The mine team were also excited about the prospect of avoiding on-board scale and loader scale maintenance going forward.
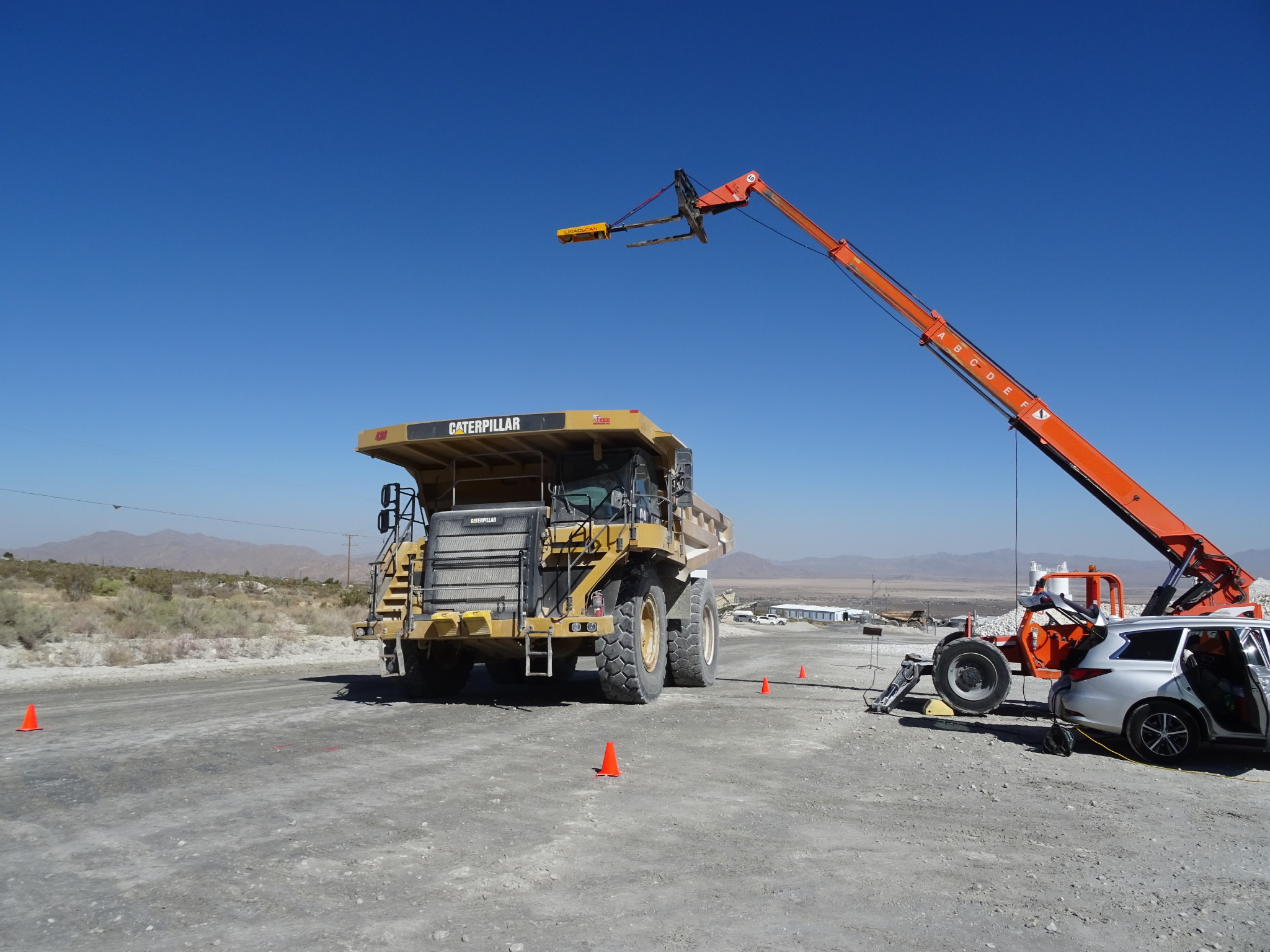
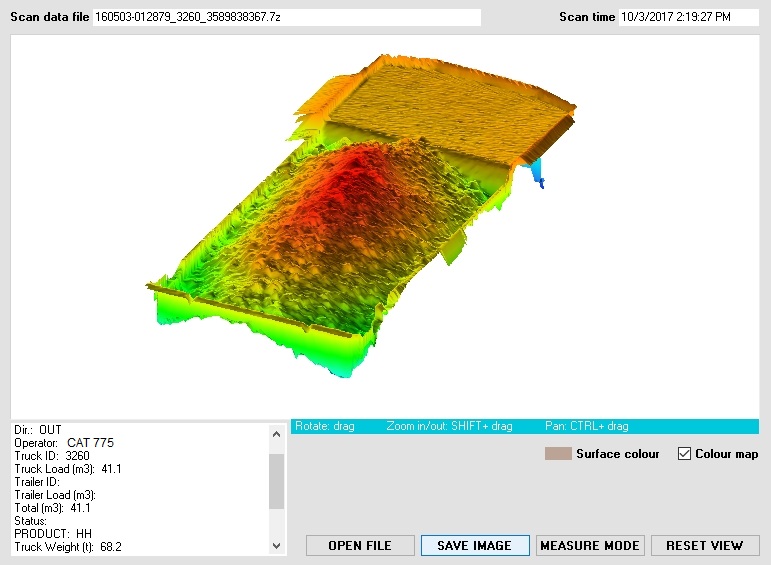
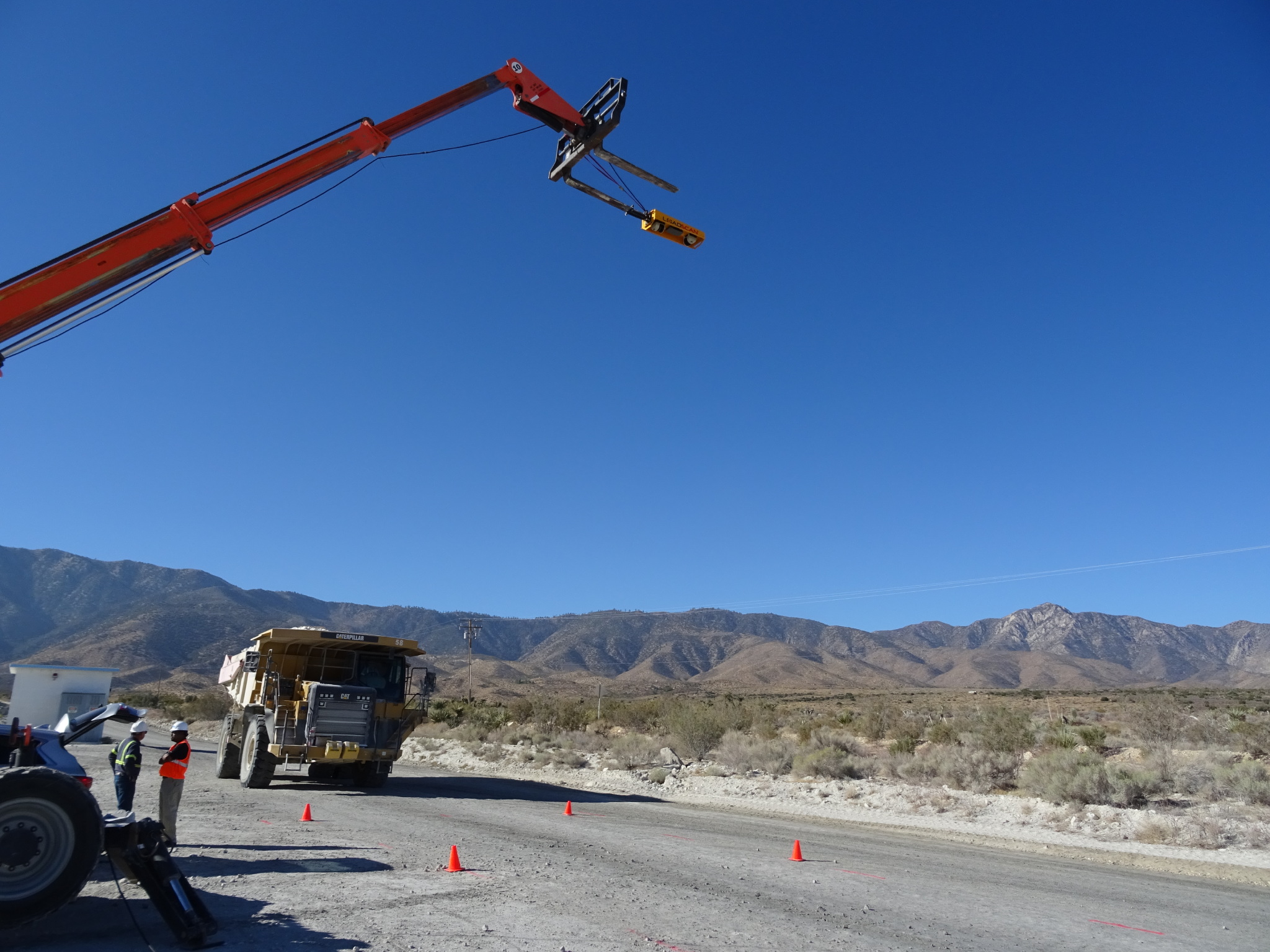
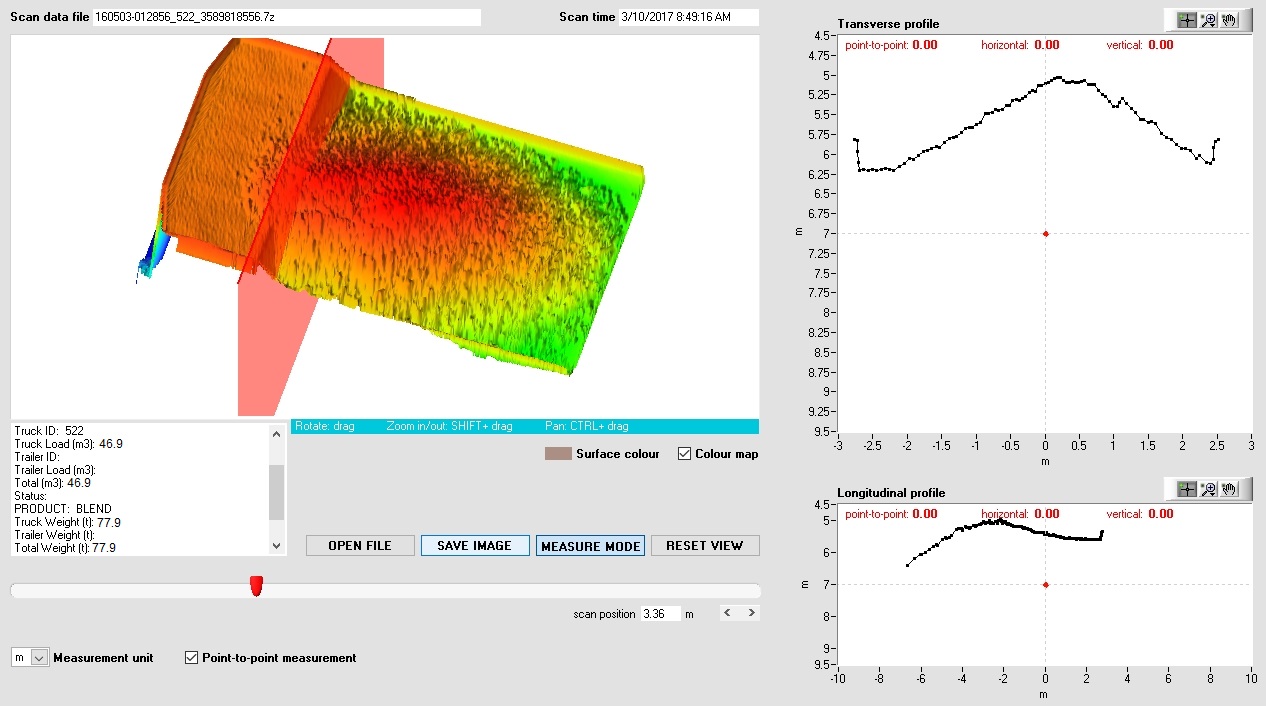